Behind every durable retaining wall is more than just good-looking block—true performance lies in what’s below the surface. Managing drainage and structural reinforcement is critical, whether you’re installing a small landscape wall or a large-scale earth retention system. These elements determine whether your retaining wall will stand the test of time or fail prematurely.
Poor drainage can lead to water pressure buildup, soil erosion, and backfill instability. Without proper reinforcement—such as geogrid, base materials, or correct abutment design—walls are at risk of settling, cracking, or collapsing.
In this guide, we’ll cover the fundamentals of retaining wall drainage and reinforcement. From key elements like drain pipes, weep holes, and soil stabilization techniques to product-specific recommendations using Rochester Concrete Products’ top-performing retaining wall systems, you’ll find everything you need to know.
Whether you’re a DIY enthusiast, a professional installer, a landscape designer, or a structural engineer, understanding the principles of block wall drainage and reinforcement will help you avoid costly mistakes and build with confidence.
Why Reinforcement and Drainage Matter in Retaining Wall Systems
Reinforcement and drainage are the foundation of a stable retaining wall. In fact, they’re just as critical—if not more so—than the concrete blocks themselves when it comes to long-term durability and protecting your property.
Wall Drainage: Crucial Relief from Pressure
Proper drainage is vital to prevent water buildup behind the wall. Without it, excess moisture saturates the backfill and dramatically increases hydrostatic pressure. This pressure can shift wall alignment, push out facing units, and eventually cause bulging, cracking, or complete structural failure.
Trapped water also undermines the soil’s strength. As fine particles wash away, voids form, leading to erosion or even collapse. In the worst cases, poor drainage can become a hidden failure point, causing wall failure, property damage, and serious safety hazards.
Wall Reinforcement: A Dual System With Drainage
Reinforcement and drainage function as a unified system to stabilize retaining walls against both hydraulic and mechanical forces. While drainage components—like drain pipes, weep holes, and drainage aggregate—manage water flow, reinforcement elements such as geogrid, proper grading, soil stabilization, and base materials resist lateral earth pressure and maintain structural alignment.
Neglecting either system compromises the entire wall.
Even the strongest reinforcement grid can’t prevent failure if the surrounding soil becomes waterlogged and unstable. Conversely, excellent drainage won’t protect a tall wall that lacks adequate soil reinforcement, especially on slopes or where heavy loads are involved.
For long-term stability and code-compliant performance, both drainage and reinforcement must work together.
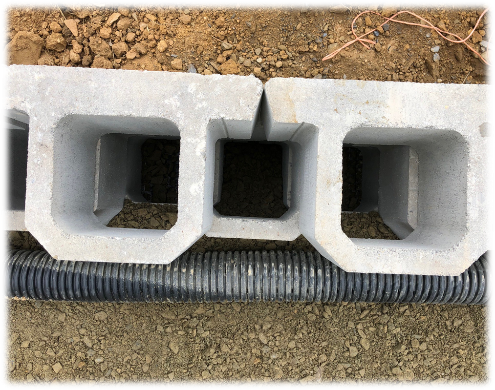
Core Components of a Retaining Wall Drainage System
A reliable block retaining wall drainage system depends on multiple components working in unison to control water flow, preserve the integrity of the backfill, and ensure long-term wall stability. Below are the essential elements that form a high-performing, well-designed drainage system for any retaining wall installation.
Backfill Materials
Backfill is the first line of defense in any retaining wall drainage system. It’s the material placed between the wall structure and the undisturbed native soil, and it plays a critical role in both drainage and structural support.
High-quality backfill promotes proper water flow and reduces pressure behind the wall. Clean, angular aggregate—such as ¾” crushed stone—is ideal, as it allows water to drain efficiently into the wall’s drainage system.
Here’s what a basic retaining wall backfill setup should include:
- Use ¾” clean crushed stone – Avoid materials like pea gravel or sand, which retain moisture and can compromise performance.
- Extend the backfill at least 12 inches behind the wall for proper drainage coverage.
- Compact the gravel thoroughly – Well-compacted backfill increases wall stability and minimizes settlement over time.
Choosing the right backfill is essential to the long-term success of your retaining wall system.
Geotextile or Landscape Fabric
Geotextile fabric—also known as landscape fabric or geotextile membrane—is a critical component in retaining wall drainage systems. It serves as a barrier between the drainage aggregate and native soil, allowing water to pass through while preventing fine soil particles from migrating into the gravel layer.
This filtration layer keeps the drainage system functioning properly and helps avoid the “honeycomb effect,” where soil infiltration creates voids, weakens the base, and risks clogging drain pipes.
A standard geotextile fabric installation includes:
- Placing non-woven geotextile fabric between the native soil and the drainage aggregate.
- Wrapping perforated drain pipes in fabric reduces the risk of clogging.
- Selecting a fabric designed to allow water flow while blocking soil particles.
Using geotextile fabric ensures your retaining wall drainage system stays clean, efficient, and effective over time.
Drainage Pipes
Drainage pipes—typically perforated PVC or corrugated plastic—are a core element of any retaining wall drainage system. Installed at the base of the wall, these pipes collect excess water and redirect it away, helping to reduce hydrostatic pressure and protect the wall’s structural integrity.
Often called longitudinal pipes or French drains, they must be laid with a consistent slope and connected to an appropriate outlet or daylighted location downslope to ensure optimal drainage and continuous water flow.
Key installation guidelines include:
- Use a 4-inch perforated drain pipe, positioned behind the lowest course of the wall.
- Wrap the pipe in geotextile fabric to prevent sediment buildup and clogging, especially important for perforated pipe systems.
- Ensure a gentle downward slope along the length of the pipe, directing water toward the ends of the wall and away from the structure.
- Provide a proper exit (e.g., to daylight or a drainage basin) so water can flow safely out of the system.
Without a reliable drainage outlet, even the best pipe installation can become ineffective over time.
Weep Holes
Weep holes are a vital drainage feature, especially for retaining walls over 4 feet tall or those constructed with facing panels, natural stone veneers, or solid block. These small openings are placed along the base course of the wall to allow trapped water to escape, helping to relieve hydrostatic pressure and prevent structural damage.
Proper placement and spacing are key:
- Install weep holes evenly along the bottom row of the wall.
- Typical spacing ranges from 6 to 10 feet, depending on the wall’s height, design, and expected drainage load.
- Ensure weep holes remain unobstructed, allowing consistent water flow to exit the system.
Incorporating weep holes into the drainage design helps preserve wall alignment, reduce soil saturation, and extend the life of the structure.
Water Sources to Monitor and Divert
An effective retaining wall drainage system doesn’t just manage water—it proactively addresses where that water comes from. Uncontrolled runoff can overwhelm even the best-designed wall system, so identifying and redirecting water sources is essential for long-term stability.
Common water sources to watch for include:
- Roof downspouts that discharge near the wall
- Surface runoff from higher elevations or sloped yards
- Improperly placed irrigation systems
- Impervious surfaces like driveways, patios, or walkways that direct water toward the wall
To manage these sources:
- Grade the site to steer water away from the wall face and toward safe drainage zones
- Connect downspouts to drainage pipes or inlets to move water away efficiently
- For larger or more complex projects, install site drainage features like swales, catch basins, or French drains to intercept and redirect water before it reaches the wall
Anticipating water flow during the design phase helps prevent pressure buildup, erosion, and other common drainage failures.
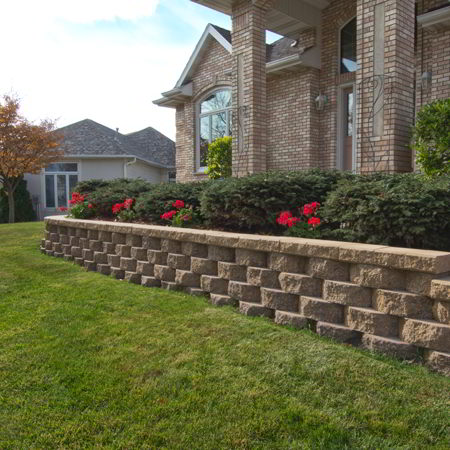
No two retaining wall projects are exactly the same, and your approach to drainage and reinforcement should reflect that. The height of the wall and the type of soil it retains are critical factors that directly impact how water behaves, how pressure develops, and how the structure must perform.
- Taller walls experience greater lateral earth pressure and require more robust reinforcement systems, such as additional geogrid layers and stronger base materials.
- Clay soils retain water and generate more hydrostatic pressure, demanding more aggressive drainage solutions.
- Sandy or well-draining soils may reduce pressure but require extra attention to prevent erosion and maintain compaction.
Tailoring your drainage and reinforcement plan to suit the site’s specific conditions ensures the wall’s long-term strength, stability, and performance.
Wall Height & Load Factors
The height of a retaining wall is a primary factor in determining the necessary drainage and reinforcement strategy. As wall height increases, so does the lateral earth pressure, making proper engineering essential to prevent structural failure.
Here’s how wall height typically impacts design requirements:
- Under 4 feet: These walls may qualify as gravity walls with little to no reinforcement, but always confirm with local building codes.
- 4 to 6 feet: Moderate reinforcement (e.g., geogrid) and layered drainage are often required, especially when slopes or surcharge loads are present.
- Over 6 feet / MSE Retaining Walls: Considered critical-height structures. These must follow a formal design by a civil or structural engineer and use full reinforcement grid systems, engineered base materials, and advanced drainage, such as multiple longitudinal drain pipes or abutment configurations. When used in civil or large-scale commercial projects, they’re often classified as Mechanically Stabilized Earth (MSE) retaining walls.
As wall height increases, drainage design must scale accordingly. Taller walls may require:
- Multiple drain pipes are placed at different elevations
- Increased outlet capacity and optimized weep hole spacing
- Concrete footings or pile systems for enhanced base support
If your wall supports additional loads—like a driveway, paver base, slope surcharge, or a fence/guardrail—it’s critical to involve a structural engineer. They can specify the appropriate reinforcement levels and drainage system layout to meet structural safety standards and local code requirements.
Soil Type Considerations
Just as wall height impacts design, so does soil type. Each soil category behaves differently in terms of drainage, compaction, and structural support, making it essential to evaluate before building a retaining wall.
Here’s how common soil types affect drainage and reinforcement needs:
- Clay-Heavy Soils
- Very low permeability; poor drainage
- High water retention leads to pressure buildup
- Requires aggressive drainage solutions and robust geogrid reinforcement
- Very low permeability; poor drainage
- Sandy Soils
- Excellent drainage with high permeability
- Low cohesion; risk of backfill washout
- Often needs geotextile fabric to keep the base stable and prevent erosion
- Excellent drainage with high permeability
- Silty Soils
- Moderately permeable but prone to compaction and settlement
- Sensitive to freeze-thaw cycles
- Must be paired with drainage aggregate to prevent water buildup
- Moderately permeable but prone to compaction and settlement
- Organic Soils
- Unstable and unsuitable for structural support
- Must be excavated and replaced with engineered fill or crushed stone
- Unstable and unsuitable for structural support
If you’re unsure about your soil, perform a simple “sandcastle test” (squeeze a damp handful—if it holds together easily, it’s likely clay or silt), or consult with a geotechnical engineer.
Regardless of soil type, using a combination of clean backfill stone, perforated drain pipe, and geogrid reinforcement helps ensure your wall remains stable and resists erosion or collapse over time.
Seasonal Considerations for Retaining Wall Drainage
Drainage systems must be built to withstand more than just heavy rain—they also need to account for seasonal changes. Shifts in temperature, fluctuating rainfall patterns, freeze-thaw cycles, and snowmelt can all impact how water interacts with your retaining wall. These seasonal forces can introduce added pressure, trigger soil movement, and test the limits of your wall’s drainage and reinforcement systems. Designing with year-round performance in mind is essential for long-term stability.
Freeze-Thaw Impacts
In colder regions, the freeze-thaw cycle is one of the most significant threats to retaining wall performance. When water becomes trapped behind the wall and freezes, it expands, exerting pressure on the wall’s face, base, and surrounding soils. Over time, this can lead to misalignment, cracked blocks, or even structural failure.
To minimize freeze-related damage:
- Ensure proper weep hole spacing to allow water to escape before freezing
- Avoid fine-grained or organic soils that retain moisture
- Use non-porous, angular drainage aggregate to promote continuous water flow
- Install drain pipes at the lowest point of the wall to prevent pooling and ice buildup
A well-drained wall is significantly more resistant to frost heave, displacement, and cracking caused by seasonal temperature shifts.
Spring Thaw & Storm Events
Spring thaw runoff and heavy rainstorms can quickly overwhelm an underbuilt retaining wall drainage system. Melting snow, paired with seasonal downpours, leads to saturated soils and elevated hydrostatic pressure, right when the backfill is at its weakest.
To protect your wall during these high-risk periods, consider the following strategies:
- Install oversized or dual-layer drain pipes to increase drainage capacity during heavy flows
- Add surface drainage inlets or catch basins to intercept runoff before it reaches the wall
- Use geogrid reinforcement systems to stabilize water-affected soils and distribute pressure evenly
- Grade surrounding landscaping to direct water away from the wall’s base and foundation
These proactive measures help relieve pressure, reduce erosion, and keep water moving efficiently through the drainage system, even during peak weather events.
Ensuring Drainage Flow in Cold Seasons
In winter, frozen pipes and surface ice can block water flow and compromise the entire drainage system. Standing water trapped in pipes during freezing conditions may cause backups, pressure buildup, or even structural damage.
To maintain drainage performance throughout the cold season:
- Use smooth-walled drain pipes, which are less prone to ice blockages than corrugated options
- Extend pipe outlets well beyond the wall base to prevent freeze-back into the structure
- Avoid terminating outlets in shaded or low-lying areas where ice is likely to accumulate
- Ensure proper slope during installation so water continues to move, even at low volumes
By designing with seasonal resilience in mind, you’ll protect your retaining wall investment all year long, from the first frost through spring runoff.
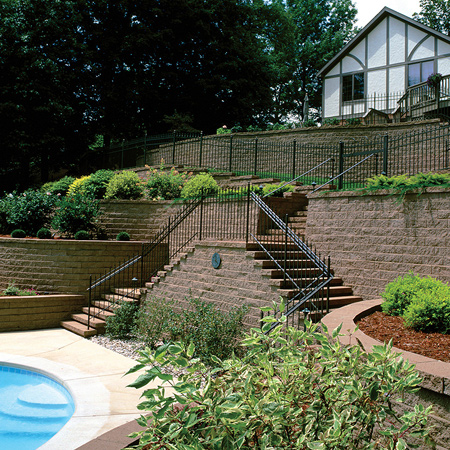
Common Reinforcement Systems in Retaining Walls
While modular block units give retaining walls their visible structure, true strength comes from what’s behind the wall. Reinforcement systems play a critical role in resisting lateral earth pressure and maintaining long-term stability.
To create a safe, load-bearing wall system, engineers commonly use:
- Geogrid reinforcement to tie the wall face into the retained soil
- Anchoring methods to secure the structure in place on challenging sites
- Strategically layered materials, including compacted backfill and base aggregates, to distribute loads and prevent shifting
These reinforcement techniques help transform stacked blocks into a durable earth retention system that can handle pressure from soil, water, and surface loads.
Key Reinforcement Methods
Reinforcement systems work by transferring pressure from the retained soil into the surrounding reinforced zone, minimizing stress on the wall face and significantly increasing the wall’s height and load-bearing potential. These systems are especially critical for walls:
- Built on slopes
- Supporting driveways or parking areas
- Subjected to heavy rainfall or poor drainage conditions
Common reinforcement methods include:
- Geogrid Reinforcement
Made from high-strength polyester yarn or polymer mesh, geogrid is installed in horizontal layers within the compacted backfill. Some geogrids are designed to mechanically lock into the retaining wall units, creating a unified system that distributes force deep into the soil mass. - Concrete Footings and Slabs
For high-load or high-exposure conditions, a reinforced concrete slab or footing may be used beneath the wall base to prevent settlement, absorb lateral pressure, and maintain alignment. - Piles, Abutment Pile Configurations, and Steel Angles
In specialized applications—such as walls near waterways, roads, or critical infrastructure—vertical steel piles or structural angles may be used to transfer forces to stable subsoil layers and anchor the wall against sliding or overturning. - Rebar and Mesh Screens
In hybrid systems that combine masonry with poured concrete cores, embedded rebar or welded mesh adds internal shear strength and helps resist cracking under dynamic loads.
These reinforcement systems, when paired with proper drainage, form the backbone of a safe and reliable retaining wall, capable of performing under varied environmental and structural demands.
Sand Castle Test
Before selecting reinforcement and drainage strategies for a retaining wall, it’s crucial to evaluate the soil conditions on-site. One quick and effective way to do this is the Sand Castle Test—a basic field test used by contractors and engineers alike.
To perform the test:
- Moisten a handful of soil and try to mold it into a small shape, like a sandcastle.
- If the soil holds its shape, it likely contains sufficient clay content to provide stability.
- If it crumbles easily or won’t hold together, the soil may lack cohesion and require additional reinforcement such as geogrid, improved backfill, or even full soil replacement.
Some installers go a step further by forming larger soil cylinders and stacking bricks on top to observe how well the soil supports weight, and how it performs when reinforced with geogrid.
Keep in mind:
- Wall height, backfill pressure, and slope conditions must be factored into any reinforcement system.
- Undersized grid layers or skipped reinforcement are leading causes of wall failure, misalignment, and costly rebuilds.
Even with a simple tool like the Sand Castle Test, you can gain valuable insight into the reinforcement and drainage needs of your retaining wall project.
RCP Drainage Design Best Practices for Block Walls
Rochester Concrete Products (RCP) has established a set of best practices to ensure that water is managed properly throughout the wall system, from the base to the surface.
Key Configurations
Proper retaining wall drainage requires a multi-layered system that manages both subsurface and surface water. This approach is essential for maintaining wall stability, preventing erosion, and ensuring long-term performance, especially when using products like Classic 6™, Premier Series, or Kodah Wall systems, which are designed to meet high structural and aesthetic standards.
Key drainage components include:
- Abutment Pile Configuration
For walls near building foundations or elevated slopes, vertical piles may be required to anchor the structure and counteract hydrostatic pressure. These deep-set supports enhance base stability in high-risk environments. - Longitudinal and Lateral Drain Integration
Base-level drain pipes (longitudinal) should be installed behind the bottom course of the wall to capture and redirect subsurface water. In combination, lateral weep holes or vertical vents provide outlets for water to escape at regular intervals, helping reduce internal pressure. - Drainage Inlets and Outlets
Surface inlets—connected to swales, roof downspouts, or catch basins—help the wall system handle larger inflows from surrounding landscape features. Outlet points must be positioned to allow free drainage away from the wall base.
Together, these elements form a cohesive drainage system that minimizes water buildup, soil saturation, and erosion, while ensuring compliance with engineering best practices.
Integration with Site Drainage Structures
One of the most common causes of retaining wall failure is overlooking external water sources. A drainage system that only addresses water within the wall footprint ignores the larger site dynamics, putting the structure at serious risk.
To ensure your wall performs as part of a comprehensive drainage strategy, consider these best practices:
- Grading
All finished landscaping should slope away from the wall to prevent surface runoff from collecting at its base. - Swales and French Drains
Install surface swales or gravel-filled trenches to intercept and redirect water around the wall, especially on sloped properties. - Downspout Tie-ins
Never allow roof downspouts to discharge near the back of a retaining wall. Instead, connect them to drain pipes or site drainage structures that route water safely away from the wall zone. - Hardscape Transitions (Guardrails & Paver Base Areas)
Where driveways, patios, or other hardscapes meet a wall, include surface drains or expansion gaps to prevent water from spilling onto or behind the structure.
These strategies ensure your retaining wall is integrated into the site’s overall hydrologic plan, not left to function as a stand-alone barrier against unmanaged water flow.
For a deeper dive into drainage and reinforcement design, download our comprehensive SRW Best Practices Guide.
Common Mistakes to Avoid in Block Wall Drainage
Even a well-constructed retaining wall can fail if the drainage system is overlooked or improperly designed. Avoiding these common mistakes is essential to ensuring long-term performance and structural integrity:
- Inadequate Backfill or Missing Filter Fabric
Using poor-quality backfill—or omitting geotextile fabric—allows fine soil particles to infiltrate the drainage zone. This leads to clogging, erosion, and eventual wall failure. - Improper Pipe Placement or Lack of Slope
Drainage pipes installed without adequate slope or without a proper outlet can trap water. This causes pooling, freezing, and added pressure behind the wall. - Ignoring External Water Sources
Irrigation overspray, roof runoff, or surface water from driveways that discharge behind the wall can overwhelm the drainage system and compromise the backfill. - No Overflow Outlets or Blocked Weep Holes
Without clear escape routes for water—such as weep holes or outlet pipes—moisture becomes trapped, saturating the soil and pushing against the wall face.
Preventing these issues starts with comprehensive site planning and a solid understanding of how water will interact with the structure throughout all seasons. Drainage isn’t just a feature—it’s a foundation of every successful, long-lasting retaining wall project.
Retaining Wall Products from Rochester Concrete Products
Rochester Concrete Products (RCP) offers a robust portfolio of retaining wall systems engineered to balance form and function. From DIY-friendly solutions to professional-grade walls designed for critical applications, each product line is built to support smart drainage integration and reliable soil reinforcement.
Classic Series
RCP’s Classic Series has been a staple in landscape and civil projects for years, known for its strength, modular flexibility, and clean architectural finish. These walls are well-suited for a wide range of applications and height requirements.
- Classic 6™ Wall: A high-performance segmental system that supports reinforcement grids and advanced drainage configurations, ideal for residential or light commercial landscapes.
- Classic 8 DOT Wall: Specifically engineered to meet local Department of Transportation (DOT) standards, this wall is designed for public infrastructure and higher-load scenarios.
- Classic Colonial 6: Blends the structural strength of Classic 6 with a split-face aesthetic for projects needing traditional visual appeal.
All Classic Series walls support geogrid reinforcement and can integrate drainage systems such as base-level longitudinal pipes, weep holes, and vertical relief zones.
Premier Series
Designed for tall or heavily loaded walls, RCP’s Premier Series delivers robust performance in the most demanding environments.
- Premier 6 Wall: A mechanically stabilized earth (MSE) wall system designed for use with engineered grid reinforcement and structured backfill—ideal for taller landscape or light infrastructure walls.
- Premier 8 Wall: This product takes everything from Premier 6 and extends height capacity, making it well-suited for MSE retaining wall applications requiring extended grid lengths, additional drainage zones, and load-bearing design.
Both are frequently used in commercial and municipal applications, where wall height and soil conditions require expert-level planning and materials.
Specialty Walls
RCP also offers unique solutions that combine structural integrity with architectural expression—ideal for modern outdoor living and landscape design.
- Barn Plank Garden Wall: Transform your outdoor area with the rustic appeal of a barn plank garden wall, which combines wooden texture and warmth with the durability and low-maintenance benefits of concrete thanks to the Silver Creek Wet Cast Technology process that can capture remarkable surface detail that can still hold up for years in harsh weather.
- Kodah Wall: Designed to replicate hand-stacked stone, Kodah delivers the rugged beauty of fieldstone with the precision of interlocking modular systems. It supports geogrid reinforcement and layered drainage designs while offering a distinctive natural look.
- Contemporary Wall: Clean, linear faces make this wall perfect for minimalist or modern landscape styles. Beneath the aesthetic, its structural capacity supports reinforced soil zones and integrated site drainage structures.
- Palisade Wall: Palisade Wall is the first single-block, facemix retaining wall in the U.S.. An enhancement to both traditional and contemporary landscapes, each block measures 40″ long, 8″ high, and 12″ deep, weighing in at 330 lbs. Available in two refined colors, Café and Cascade, this system features two unit types delivered on separate pallets: Standard Units with facemix on the front and Corner/End Units with facemix on the front and one end.
- Olympic Wall: Transform your outdoor space into a modern oasis. Olympic Wall features a sleek design with dramatic beveled edges, offering unparalleled modern elegance.
- Lakeland Wall: The Lakeland Wall features a rugged texture and the timeless look of natural stone. Lakeland is ideal for creating graceful curves, straight lines, or tiered walls in both residential and commercial settings.
These walls offer both aesthetics and top performance under real-world conditions where soil type, wall height, and moisture exposure intersect.
Backed by Expertise
RCP’s wall systems are supported by decades of field-tested engineering and technical resources.
Whether your project is guided by a structural engineer or a seasoned contractor, RCP’s wall products provide the modular flexibility, drainage reliability, and structural reinforcement needed for lasting results.
Build Smart, Drain Better for Walls That Last
Retaining walls should do more than define space—they must be engineered to manage water, resist soil movement, and withstand the test of time and weather. Whether you’re building with concrete block or another material, long-term success starts with a thoughtful plan for effective drainage and reinforcement.
From clean backfill and geotextile membranes to properly placed weep holes, drain pipes, and geogrid reinforcement, every element plays a role in maintaining wall stability and protecting your investment.
Most importantly, tailoring your design to site-specific factors—like wall height, soil conditions, and surrounding water sources—helps you avoid common failures such as erosion, frost damage, and structural shifting.
By focusing on these core principles, you can build retaining walls that are not only visually appealing but also structurally sound for years to come.
Why RCP is the Trusted Choice
Rochester Concrete Products offers more than just retaining wall blocks — they provide solutions for everything from gravity retaining systems to geogrid retaining designs. With American-made quality, engineered product lines, and resources like the Segmental Retaining Walls Best Practices Guide, RCP supports both homeowners and professionals in constructing reinforced soil structures and reinforced earth retaining systems. Whether you’re working on a concrete retaining or concrete block wall, incorporating geogrid reinforcement can help stabilize a slope or soil wall for long-term durability. RCP delivers the knowledge and products you need to build smarter, safer, and more confidently.
- Made-in-USA durability: All products are designed and manufactured to handle real-world environments, including freeze-thaw climates and varied soil conditions.
- Warranty-backed reliability: Every system is supported by structural integrity standards and long-term performance assurance.
- Technical guidance and support: From downloadable specs to CAD files and installation checklists, RCP supports every phase of the project, from design to build.
When drainage and reinforcement are done right, your wall won’t just look great but also last for decades. That’s the RCP difference.